At a glance
- Client: Basalt AG
- Industry: Building Industry
- Project objective: Implementing a cloud platform with Microsoft Fabric for the business use of IoT data
- Technologies: Microsoft Fabric
Basalt AG’s products are quite literally fundamental to our society’s mobility. A significant share of the asphalt on German roads originates from the company’s quarries and production sites. The same applies to the track ballast that provides the basis for our railroads. Basalt covers the entire supply chain from raw material extraction to provision at the point of use, as well as recycling and disposal.
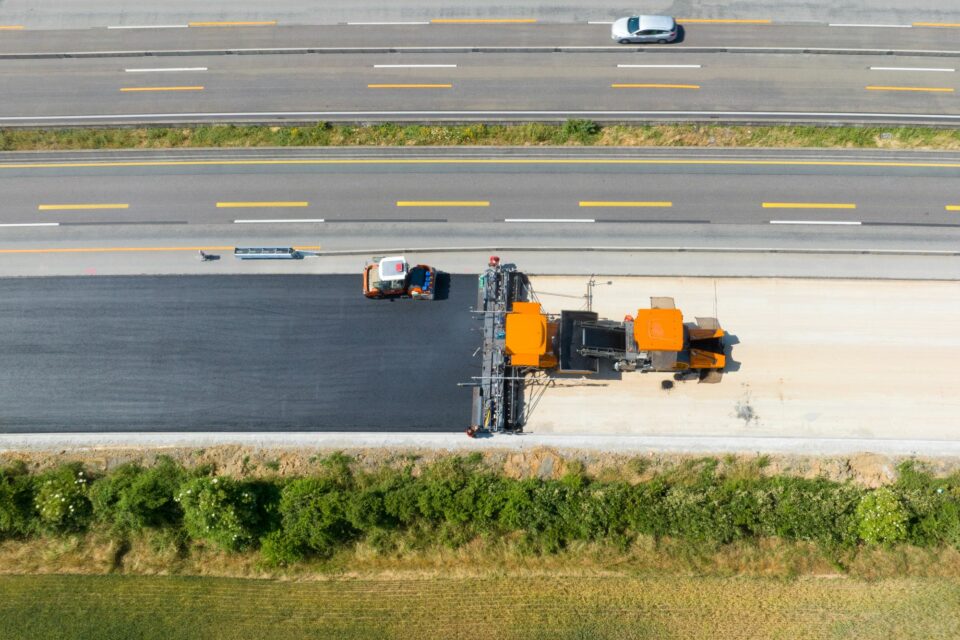
A considerable share of the asphalt laid in Germany originates from Basalt plants. (Basalt AG)
As a result, sustainability-related topics play a major role at Basalt. At the same time, they are also posing the greatest challenge: It is not only about meeting the continually growing demands of the government and the public. Sustainability is in fact a key factor in production within the natural stone sector and is therefore one of the most important business objectives. Improvements in this area always can potentially create a competitive edge for the company in economic terms as well. However, how do we manage to further promote sustainable actions in this day and age?
Those in charge at Basalt already have the answer to that question: “We simply have to make use of the wide range of data resources available to us across the entire supply chain,” says Heiko Bornemann, Head of IT infrastructure. “Currently, this treasure trove of data is scattered across almost 300 locations in Germany, buried within various systems and data silos.” This is why the company has decided to launch a large-scale digitalization initiative aiming at centralized data that can be made available for various types of application scenarios across the company.
Digitalization = Industry 4.0
At Basalt AG, digitalization means a commitment to the implementation of Industry 4.0 and its very foundation, the Internet of Things (IoT). This is because, until now, the extensive data streams from large stone crushers, for example data on capacity utilization and productivity, have not yet generated any business value. Heiko Bornemann explains: “In the future, we want to combine the sensor data from all plants in an Operational Data Management System and then link it to the rest of our company data. Of course, the data should then be made available for business applications in real time if possible.”

The extensive data streams at the Basalt quarries have not yet generated any business value until now. (Basalt AG)
Basalt is not only hoping for better decision-making and a number of new insights. The company also intends to use the Operational Data Management System to further interconnect people and machines as well as to digitalize and automate processes. Heiko Bornemann underscores that Basalt is not only focused on sustainability targets: “We are also facing site-specific challenges such as the generational change and a shortage of skilled labor. We consider automated processes to be a lever, helping us to break down knowledge silos and to deploy our valuable staff in a more efficient manner.”
With these requirements in mind, Basalt started its search for a suitable data technology and the right partner to implement it. One thing was unnegotiable from the beginning: It has to be a Microsoft solution because the existing systems are already running in the Azure Cloud.
Microsoft Fabric is the base technology
During their research, the team repeatedly came across Fabric – Microsoft’s brand-new technology approach that allows a complete data platform to be rolled out and ready to use at the touch of a button. “We had already attended a presentation in Munich,“ says Heiko Bornemann. “To us, it sounded like the ideal concept, since we are hoping for a high degree of autonomy and would like to do as many things ourselves as possible.” After an individual presentation by Microsoft, Basalt opted to trial Microsoft Fabric within a sponsored Proof of Concept (POC), as, although the technology is currently celebrating its first notable practical successes in many areas, it has so far only had limited opportunities to prove itself in Industry 4.0 scenarios.
When it came to choosing the ideal partner, ORAYLIS GmbH was able to impress Basalt by focusing on the essentials: “We had conversations with several service providers. Ultimately, to me, the decisive factor was the fact that the ORAYLIS consultants quickly grasped our use case and shared tangible ideas, instead of jumping straight to huge digital twin concepts. Additionally, ORAYLIS boasts proven Fabric expertise. Thanks to its early involvement in introducing and promoting the technology, Microsoft recently selected ORAYLIS as one of its few “Fabric Featured Partners” in Germany.
Real-time sources can be integrated smoothly
The basic objective of the PoC was to link plant data with standard business data for the first time and to visualize the results on a dashboard in near real time. This meant bringing together all key interest groups involved in company-wide digitalization. In addition to representatives from IT infrastructure, these included the “Central Technology” department, which is responsible for machine systems, and the “Industry Solutions” department, which is in charge of operational systems.
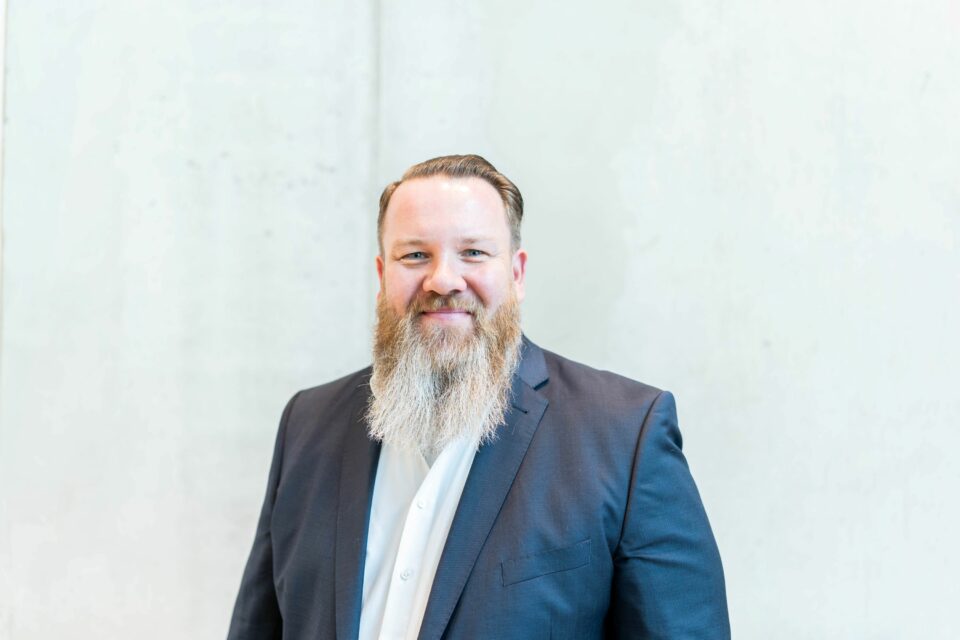
Fabric expert Dirk Ohligschläger was part of the project as solution architect. (ORAYLIS GmbH)
Dirk Ohligschläger, Senior Solution Architect at ORAYLIS, describes the next steps as follows: “We first set up our central platform using Fabric, which was very easy. It actually only takes a few steps to set up the entire architecture, including data integration, processing and the respective analysis tools.” Afterwards, the platform was linked to the four pilot plants. “The bridge between stone crusher and platform serves as an edge device. It receives the data streams from the plant sensors and feeds them directly into our cloud database. And just like that, we were able to see the first real numbers in Power BI after just a short time. The integration process was completely trouble-free.”
Our Fabric expert has only reported a few minor hitches along the way to the first real-time results at Basalt: “At one point, we exceeded our capacity limits, which led to Reporting being down for a few hours. However, that was simply a matter of configuration. Moving forward, we’ll know better. In my opinion, Fabric has clearly passed our IoT test.”
Expectations were in fact exceeded
Heiko Bornemann, too, is highly pleased with the PoC’s progress: “We are truly impressed with how quickly we were able to achieve the desired results. In the end, our expectations were in fact exceeded. It doesn’t stop with feeding data from the stone crusher to the dashboard via the cloud; ORAYLIS has already integrated filters for specific sites and set up a dashboard for individual figures.” At the same time, another business case was implemented; an energy monitoring system which critically analyzes the plants’ energy consumption. This system will also be a fixed part of the Operational Data Management System.
According to Heiko Bornemann, the teamwork between Basalt and ORAYLIS was one of the project’s main success factors: “It was a perfect match, especially since we lack the necessary expertise in data processing and the linking of new sources. The consultants at ORAYLIS don’t keep their expertise to themselves. The whole team has benefited from them sharing their knowledge. This is why it is safe to say that ORAYLIS was the missing piece of the puzzle for us to successfully implement a project of this kind.”
Driving digitalization with purpose
At the same time, the work of the dream team has already generated appetite for more among the company: “Our colleagues, especially those working on the Operational Data Management System, were already showing great enthusiasm before the PoC had even ended. They were keen to immediately get started on validating even more data and introducing further requirements. This was of course highly motivating for us. However, we have to make sure to not get carried away too quickly, because we are not working with a live system yet.”
To Heiko Bornemann, that means to pause for a moment and take stock: “I believe that by introducing the Fabric platform, we laid the ideal foundation for gradually digitalizing our company. We see huge potential, especially in terms of Predictive Maintenance and Alerting. We will analyze the PoC’s results precisely and then structurally integrate further data and approach new use cases. The course of action is now clearly defined.”
turn your data into value.